Briques en terre cuite: composition, propriétés et technologie de production
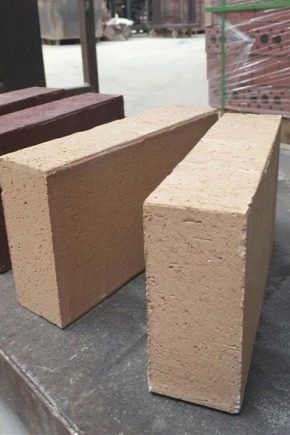
La production de matériaux de construction est une activité attrayante et prometteuse, car ces produits seront toujours en demande. Mais il est important d'organiser l'ensemble du processus selon des règles technologiques strictes. Ayant raté au moins un moment, il est impossible d’obtenir une brique ordinaire en argile.
Préparation des matières premières
La première étape consiste naturellement à fournir des installations de production en matières premières. La recherche de dépôts d'argile est effectuée à l'aide de méthodes d'étude géologique standard. Lorsque des couches sont trouvées, les experts évaluent leur puissance, ressources disponibles pour la fabricationSi une décision est prise d'utiliser une carrière spécifique, la zone est nettoyée à l'avance (1 à 2 ans supplémentaires). Il devrait être libéré de la végétation et des races évidemment inutiles.
Souvent, la surface du sol est relâchée pour simplifier l'extraction ultérieure. Au même stade, les lignes de transport et d'énergie sont amenées dans la carrière (en l'absence de communications prêtes). Extraction de l'argile produite par:
applications des excavatrices;
broyage d'explosifs de roche;
avec l'utilisation de voitures relativement petites (bulldozers et ainsi de suite).
Types de produits
La production de différents types de briques suggère des différences significatives dans la technologie du produit, même s'il s'agit de produits de la même taille.
La brique à double silicate est meilleure que la céramique en isolation phonique, mais inférieure en ce qui concerne ces indicateurs:
résistance au froid;
stabilité thermique du bâtiment;
absorption d'humidité.
Dans le même temps, la brique rouge traditionnelle est plus chère. Sa production nécessite des équipements plus coûteux, dure beaucoup plus longtemps. La complexité est également accrue, ainsi que la consommation d'énergie.Mais dans les deux cas, la matière première traverse plusieurs étapes. Tout d’abord, préparez la masse d’argile en lui donnant les caractéristiques nécessaires.
Puis moulé brut, séché. Et alors seulement vient le moment de la mise à feu, c’est-à-dire la principale opération technologique. Afin de bien exécuter les travaux, les roches d'argile qui sont entrées dans la briqueterie sont triées conformément à GOST 1975.
Cela prend en compte:
propriétés réfractaires;
capacité de frittage;
composition minérale;
propriétés plastiques;
résistance mécanique à l'état sec.
Les caractéristiques chimiques des matières premières impliquent la détermination de la concentration:
sels solubles dans l'eau;
l'alumine;
composants à grains grossiers;
fines fractions dispersées;
oxyde de fer;
dioxyde de titane;
silice libre.
Caractéristiques du processus
Les matières premières d'argile, venant de la carrière, conviennent rarement à la fabrication de produits de qualité. Pour améliorer la qualité des matières premières, il est nécessaire de les soumettre à un traitement météorologique, climatique et mécanisé. La première étape consiste à laisser le mélange d'argile dans des conditions contrôlées pendant un à deux ans.Cette période est nécessaire pour le mouillage, la congélation et la décongélation (parfois le processus de congélation et décongélation est effectué plusieurs fois), pour les intempéries. Lorsque cette procédure se termine, ils sont usinés.
Cela implique:
des modifications minutieuses de la structure des matières premières;
fragmentation de l'argile, inclusions étrangères dans celle-ci;
nettoyage des grosses inclusions et des impuretés;
mélanger l'argile jusqu'à consistance lisse.
La préparation technologique de la masse d'argile est réalisée à l'aide de diverses machines spéciales. Certaines personnes détachent l'argile, d'autres le frottent, d'autres se désintègrent (sans pierres de différentes tailles). Les broyeurs à boulets et rotatifs, les mélangeurs d'argile et les mélangeurs à hélice sont également utilisés dans les briqueteries. Il existe également des appareils de production multifonctionnels.
Mais ils ne peuvent remplacer que des installations individuelles et non la chaîne de production dans son ensemble.
Comment est moulé l'argile
Dans la plupart des cas, une technique plastique est utilisée. Il permet de traiter des matières premières de plasticité moyenne, dont l'humidité varie de 18 à 28%. Pour cela, une presse à bande est utilisée.Il est recommandé d'utiliser des presses capables de chauffer la masse d'argile sous vide.
Ce mode de traitement augmente la force du brut.
Il y a aussi une technique difficile. Il est considéré comme un sous-type de procédé de traitement plastique. Cette approche est appliquée à une masse d'argile relativement grossière avec une teneur en humidité de 13 à 18%. Des presses hydrauliques sont utilisées pour le traitement difficile de l'argile. Des machines avec chambres à vis et à vide peuvent également être utilisées. À la fois en plastique et en brique dure, la masse non cuite doit être coupée en morceaux à la fin du processus de moulage.
La méthode de production de flans semi-secs est relativement rare. Il est utilisé lorsqu'il est nécessaire de traiter des matières premières insuffisamment plastiques, appelées argiles maigres. Cette matière première a une teneur en humidité de 8 à 12%. Le temps de traitement total est réduit. La méthode de production à sec implique la formation de briques à partir de poudre d'argile avec une teneur en humidité de 2 à 6%.
Il n'est pas nécessaire de le sécher, à partir de matières premières telles que vous pouvez obtenir les produits céramiques les plus denses.
Séchage
D'une manière ou d'une autre, lorsque les briques sont formées, il est généralement temps de les sécher.Lors de cette phase de traitement, une diminution de l’humidité de 5 à 6% est obtenue. Si vous ignorez cette exigence et envoyez des produits humides au four, ils peuvent se fissurer et même se déformer. La production dynamique moderne ne peut plus se permettre un séchage naturel durable. Pour accélérer le processus à l'aide de séchoirs à chambre ou à tunnel.
Et afin d'accroître l'efficacité technique et économique de la production, il devient de plus en plus le choix d'installations en continu.
Dernière étape de traitement
La température de cuisson des briques requise est créée dans différents types de fours - le plus souvent en tunnel et en anneau.
Le tir est divisé en trois étapes plus petites:
Réchauffer le bloc d'argile préparé;
effets de température appropriés;
abaissement planifié et progressif de la température.
Dans la première étape, la pièce est chauffée à 120 degrés. Ceci conduit à l'évaporation des effets physiques associés à l'humidité. Le produit devient beaucoup moins plastique. Dès que la température atteint 600 degrés, ce changement devient irréversible. L'évaporation de l'humidité résiduelle se produit et l'argile acquiert une structure amorphe. La matière organique finira par brûler.
Dès que la brique est chauffée à 800 degrés, les bords extérieurs des particules de la pièce sont étroitement imbriqués. Cela permet à la brique finie de devenir plusieurs fois plus forte. Lorsque la température atteint 1000 degrés, l'heure du retrait au feu est venue. Les produits finis sont frittés et deviennent plus denses. Les substances facilement fondantes, devenues liquides, enveloppent ce qui n’a pas encore fondu - en même temps, en plus de réduire le volume de 2-8%, la résistance mécanique de la brique augmente légèrement.
Pour apprendre à fabriquer une brique d’argile avec vos propres mains, regardez la vidéo ci-dessous.